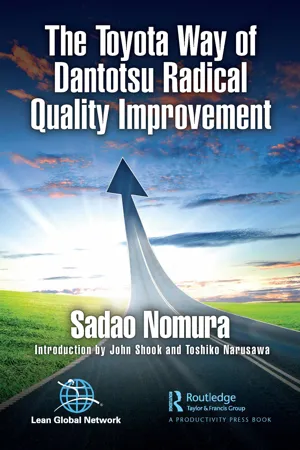
The Toyota Way of Dantotsu Radical Quality Improvement
Sadao Nomura
- 276 páginas
- English
- ePUB (apto para móviles)
- Disponible en iOS y Android
The Toyota Way of Dantotsu Radical Quality Improvement
Sadao Nomura
Información del libro
In this book, author Sadao Nomura taps into his decades of experience leading and advising Toyota operations in a wide variety of operations to tell the story of radical improvement at Toyota Logistics & Forklift (TL&F).
This book tells in great detail what the author did with TL&F, how they did it, and the dramatic results that ensued. TL&F has long been a global leader in its industry. TL&F is part of Toyota Industries Corporation, which was founded by Toyota Group founder Sakichi Toyoda almost 100 years ago. Sakichi Toyoda is legendary in the Lean community as the originator of the all-important "JIDOKA" pillar of TPS, which ensures 1) built-in quality and 2) respect for people through ensuring that technology works for people rather than the other way around. Although TL&F seemed to be performing well, insiders knew that, as the founding company of the Toyota group, it needed to do better, especially in the quality performance of its global subsidiary operations. But improvement would not be easy in a company that already prided itself in its history as an exemplar in providing highest quality products and services.
In 2006, TL&F requested assistance from Sadao Nomura. The initial request was for Mr. Nomura to support quality improvement in three global operations that had become part of TL&F through acquisition: US, Sweden, and France. Improvement was expected at these affiliates, but the dramatic nature of the improvement was not. Further, the improvement activities were so powerful that they were also instituted at the parent operations in Japan. Over a period of almost ten years, the company with the name most associated with product quality experienced quality improvement unparalleled in its history. "Dantotsu" means "extreme, " "radical, " or "unparalleled."
Preguntas frecuentes
Información
Part 1
Target Setting
Chapter 1
Setting concrete targets to achieve zero defects
1. Flow of quality information and definition of defects


- Not only users in the marketplace, but also subsequent process workers should be regarded as “customers”!
- The outflow of quality defects to the subsequent process causes major inconveniences such as interruption of work and/or reworking of defects. Therefore, it is necessary to tackle zero outflow of any defects to anywhere including subsequent processes.
- Leadership in the quality assurance department is extremely important. In order to deliver products with zero quality defects to customers in the market, we need activities that can assure quality throughout all processes of the supply chain from material suppliers (first process) to dealers (final process). Therefore, the role of the quality assurance department, which is responsible for cross-sectional quality management, is very important.
2. Target Setting
(1) Target setting for vehicle manufacturing plants
1) Target: Reducing the market claim costs (example)

- The general managers of technical and manufacturing departments broke down their respective department targets, determined individual sections’ targets within each department, and instructed each section manager to start the three-year Dantotsu Quality Activities.
- The quality assurance department prepared a market claim amount chart for 2006 by supplier. For the top-thirty suppliers that showed the worst results, the department presented a 50-percent reduction target to each company, and supported the claim reduction activities.
2) Target: Reducing the number of defects per vehicle in finished vehicle inspections (example)

- The target for each section was based on the 2006 results for the number of defects per day because the value would become too small if it were based on the number of defects per vehicle. Setting the reference values in parentheses as targets makes it easier for on-site workers to understand the targets. Each section manager decided this and informed all members in the individual sections. (Chart 1-4)
3) Target: Reducing the number of supplier-related* defective deliveries

- The quality assurance department checked the number of defective deliveries from suppliers in FY 2006 and prepared a worst suppliers list. For the top-thirty worst suppliers, the department set Dantotsu activity targets, presented respective targets to each company, and supported their reduction activities. (Charts 1-5 and 1-6)
- * “Supplier-related” means “the suppliers were responsible for the defects”.
