
eBook - ePub
Additive Manufacturing
Science and Technology
Emrah Celik
This is a test
Compartir libro
- 151 páginas
- English
- ePUB (apto para móviles)
- Disponible en iOS y Android
eBook - ePub
Additive Manufacturing
Science and Technology
Emrah Celik
Detalles del libro
Vista previa del libro
Índice
Citas
Información del libro
This book covers additive manufacturing of polymers, metals, ceramics, fiber reinforced polymer composites, energy harvesting materials, and biomaterials. Hybrid manufacturing is discussed. Topology optimization methodology is described and finite element software examples are provided. The book is ideal for graduate students and career starters in the industry.
Preguntas frecuentes
¿Cómo cancelo mi suscripción?
¿Cómo descargo los libros?
Por el momento, todos nuestros libros ePub adaptables a dispositivos móviles se pueden descargar a través de la aplicación. La mayor parte de nuestros PDF también se puede descargar y ya estamos trabajando para que el resto también sea descargable. Obtén más información aquí.
¿En qué se diferencian los planes de precios?
Ambos planes te permiten acceder por completo a la biblioteca y a todas las funciones de Perlego. Las únicas diferencias son el precio y el período de suscripción: con el plan anual ahorrarás en torno a un 30 % en comparación con 12 meses de un plan mensual.
¿Qué es Perlego?
Somos un servicio de suscripción de libros de texto en línea que te permite acceder a toda una biblioteca en línea por menos de lo que cuesta un libro al mes. Con más de un millón de libros sobre más de 1000 categorías, ¡tenemos todo lo que necesitas! Obtén más información aquí.
¿Perlego ofrece la función de texto a voz?
Busca el símbolo de lectura en voz alta en tu próximo libro para ver si puedes escucharlo. La herramienta de lectura en voz alta lee el texto en voz alta por ti, resaltando el texto a medida que se lee. Puedes pausarla, acelerarla y ralentizarla. Obtén más información aquí.
¿Es Additive Manufacturing un PDF/ePUB en línea?
Sí, puedes acceder a Additive Manufacturing de Emrah Celik en formato PDF o ePUB, así como a otros libros populares de Technologie et ingénierie y Sciences appliquées. Tenemos más de un millón de libros disponibles en nuestro catálogo para que explores.
Información
1 Introduction
1.1 A disruptive technology, additive manufacturing
Additive manufacturing (AM) is a revolutionary technology, which is based upon building three-dimensional (3D) objects by adding successive layers of material. Different types of materials can be fabricated with this technology, including polymers, metals, ceramics, composites, or biological materials. Since AM allows fabrication of parts in complex geometries without the use of any tooling, early use of AM focused on visualization models in the form of rapid prototyping. Due to the significant improvement in material library and the quality of the fabricated parts, AM has recently been used to fabricate end products in aerospace, dentistry, medical implantation, automotive, and even fashion design.
Unlike traditional subtractive manufacturing, AM is the process of joining materials to make objects layer by layer. In the past century, subtractive manufacturing has made a great impact on fabrication and prototyping since it was first introduced. Now, manufacturing industry is on the verge of a new revolution due to the new design and fabrication opportunities offered by AM. Figure 1.1 shows the major differences between the subtractive manufacturing and AM technologies. Subtractive manufacturing, as its name implies, involves removing sections from a material by machining or cutting it away. It can be performed manually or via computer numerical control (CNC) machining. AM is also a computer-controlled process but unlike subtractive manufacturing, it adds successive layers of material to create a 3D object.
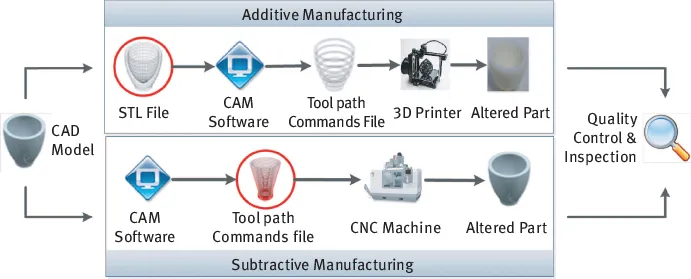
Figure 1.1: Additive versus subtractive manufacturing. Figure was reprinted from [1].
Traditional subtractive manufacturing, in general, has benefits of cost per part (especially for a high-scale manufacturing), speed, component strength, and material selection. New AM technologies however quickly close the gaps in these areas and bring up a new design space involving on-demand fabrication, creation, customization, and complexity redefining current manufacturing.
As it will be described in the next section, there are many AM technologies developed for different manufacturing purposes. Despite their differences, all AM methods share common processing steps as illustrated in Figure 1.2. The AM process starts with the design of the component using a 3D computer-aided design (CAD) modeling software. The model can also be constructed via reverse engineering using a 3D scanner or photography. Once the computer model is created, it is transferred into a slicing software where 3D model is digitally converted into serial 2D sections format. The AM equipment then reads this data and lays down successive layers of liquid, powder, sheet material, or other forms layer-by-layer to fabricate a 3D object. Minimum layer thickness dictates the manufacturing quality and it depends on the machine and AM process type selected. Finally, additively manufactured object is removed from the AM instrument and, if desired, postprocessing such as cleaning, sanding, coating, painting, compacting, or heat treatment is applied to enhance component performance or esthetic appearance. Postprocessing may involve the use of other machines and tools.
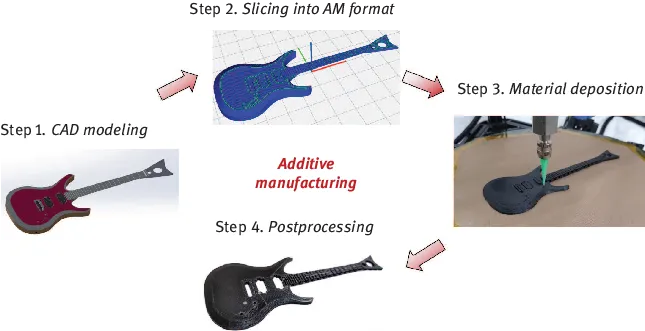
Figure 1.2: Main processing steps of additive manufacturing: CAD modeling, AM format slicing, material deposition, and postprocessing.
1.2 Advantages of AM over traditional manufacturing
AM finds unique applications in vast variety of fields including electronics, aerospace, automotive engineering, and even fashion design as shown in Figure 1.3. This is due to the advantages of AM over traditional manufacturing technologies.
These benefits are summarized as follows:
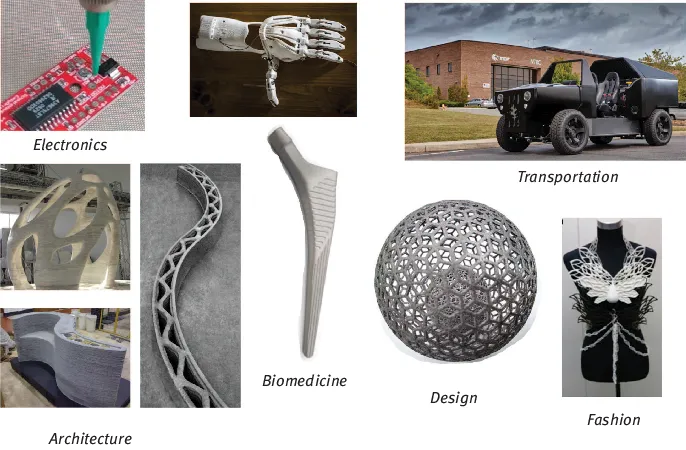
Figure 1.3: Various applications of additive manufacturing. Concrete printing (architecture) [2], transportation, [3], and fashion [4] application images were reprinted with permission.
1.2.1 Greater design ability
AM systems allow fabrication of moving parts (hinges, chains, etc.) in a single print process, and complex structures are unachievable with the traditional manufacturing. In addition, due to the flexibility of design, traditional constraints of manufacturing are eliminated and number of parts in the design can be reduced. Redesign process can be done digitally on the CAD model and the new part can be fabricated in a short period of time. Since AM is a user-friendly technology and not labor intensive, the designers are not limited to only engineers but variety of makers such as architects, artists, and even students adopt this technology in making things. Therefore, AM technologies have created a new design space and found a great interest in the community we live in.
1.2.2 No tooling
In AM, unlike many traditional manufacturing techniques, jigs, fixtures, or molds are not required to secure and shape the parts being made. The components are fabricated directly on a printbed or an already-fabricated part. This is a huge cost-saving avenue of AM considering expensive tooling of traditional manufacturing systems.
1.2.3 On-demand manufacturing
Parts can be fabricated anytime as soon as the CAD model is prepared. These CAD models can also be sent digitally and the manufacturing can be done at home or remote locations near consumers eliminating the transportation of the fabricated parts.
1.2.4 Rapid prototyping
Compared to the conventional techniques with more geometric limitations, AM can produce models quickly, in hours instead of weeks. The makers/designers can test the prototypes quickly to save significant amount of time in the design process to achieve the final product.
1.2.5 Customization
Every part can be fabricated differently with the AM process without adding the cost of fabrication. The customization can be particularly useful for the biomedical applications, where each part can be fully customized for different patients and their special requirements.
1.2.6 Minimal material waste
Since AM technology is based on adding material to build the 3D object rather than material removal, it uses the exact amount of material to produce parts and there is usually no waste of material. Support material and extra powder used during the process can often be recycled and reused for the production of the next part. This would reduce material cost due to material waste and waste removal. This would also minimize the environmental implications stemming from the waste in conventional manufacturing.
1.2.7 Low cost for small number of parts
With the advancement of technology, AM systems are becoming more affordable and more portable compared to the traditional manufacturing systems. Low investment costs of the AM machines attract more interest on these systems. The cost of fabrication depends highly on the number of fabricated parts and complexity. Usually, traditional manufacturing is beneficial for fabrication of high number of geometrically simple parts, whereas AM becomes highly competitive or even cheaper for manufacturing of low number of parts with high complexity.
1.3 Classification of AM technologies
There are numerous AM technologies used for the fabrication of different materials. In 2010, the American Society for Testing and Materials (ASTM) group, formulated a set of standards that classify the range of AM processes into seven major categories as shown in Figure 1.4 [5]. Each of these seven methods significantly varies in their method of layer-by-layer AM. Each of these categories is explained as follows.
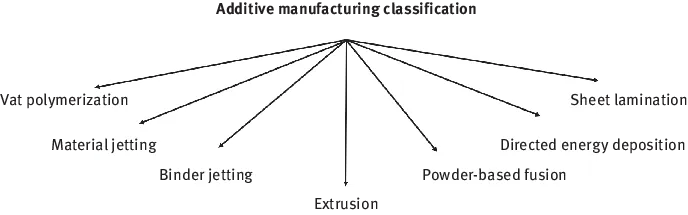
Figure 1.4: ASTM classification of additive manufacturing technologies.
1.3.1 Vat polymerization
Vat polymerization (a.k.a Vat photopolymerization) is a 3D printing technology, which relies on selectively curing a liquid photopolymer contained in a vat (or tank) by a light source. Light is used to cure or solidify the resin where required, while a platform moves the built object downward (or upward) after each new layer is cured. The process continues curing the photopolymer layer by layer until building of a 3D physical object is completed. After completion, the resin in the vat is drained and the object is removed. Usually, photopolymerized samples are postcured under ultraviolet (UV) light to achieve complete curing and maximum strength.
The majority of the photocurable resins consist of mixtures of monomers combined with oligomers (a few units of monomers) and photoinitiators. As shown in Figure 1.5, oligomers and monomers are disconnected in uncured liquid photopolymer resins. As UV light is applied on these photopolymers, photoinitiators are activated and cross-link the monomer and oligomer units. This chemical process, known as photopolymerization or photocuring, transforms liquid photopolymers into solid components.
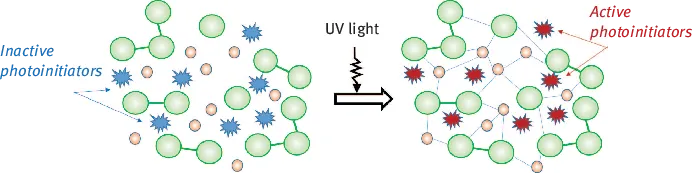
Figure 1.5: Schematic of photopolymerization process.
Depending on the type of photoinitiator and the polymerization process, there are two major photopolymerization types: (1) free-radical polymerization and (2) ionic photopolymerization. Free-radical photopolymerization is commonly used in photopolymerization-based AM technologies (Vat polymerization, material jetting). Free-radical photopolymerization process takes place in multiple steps including activation of the photoinitiator upon exposure to radiation within an appr...