
Building a Sustainable Lean Culture
An Implementation Guide
Tina Agustiady, Elizabeth A. Cudney
- 240 páginas
- English
- ePUB (apto para móviles)
- Disponible en iOS y Android
Building a Sustainable Lean Culture
An Implementation Guide
Tina Agustiady, Elizabeth A. Cudney
Información del libro
This book is an implementation guide for creating a Lean Culture from the ground up while gaining buy-in from key stakeholders and being able to sustain the results. Everyone talks about implementing a Lean Culture, but only provides Lean Tools for the implementation. This book discusses implementing the entire system from three main aspects. It will cover the people (structural and cultural), the operation system, and the tools. Also included is a full set of case studies to show real-life implementations as well.
This text-
-
- Discusses Leader Standard work for all employees
-
- Covers the escalation process for tiers and daily accountability
-
- Shows how to deal with a change of SOP's and standardization within an organization
-
- Presents exercises for Lean Tools Implementation
-
- Offers real-life case studies of implementing a lean culture while sustaining it
Building a Sustainable Lean Culture: An Implementation Guide discusses Lean Leadership from a managerial standpoint and ensures the lean journey does not fail through accountability, standardized work, and technological advances utilizing Lean Systems.
Useful in manufacturing, services, IT, and healthcare, this book includes the implementation of empowering employees to want to build a Lean Culture.
Preguntas frecuentes
Información
1 Introduction to Lean and the Importance of Cultural Change
A strategy that is at odds with a company’s culture is doomed. Culture trumps strategy every time.—Jon R. Katzenbach, Ilona Steffen, and Caroline Kronley
Lean Overview
- Lean is NOT the next headcount reduction exercise.
- BUT: Lean creates opportunities for doing more value-added activities.
- Lean will not succeed if the initiative stays limited to “operations.”
- Lean is NOT about working harder, but rather working smarter.
- Quality is inherent in Toyota’s products.
The company is constantly striving for improvement (Kaizen), which has direct benefits for their customers. Toyota’s insistence on maintaining quality throughout the production process is vital to ensuring that their finished products are of the highest quality. - Cost is always an issue.
By buying Toyota products, their customers can be sure they have made a good choice. Kaizen ensures that Toyota products feature the latest effective innovations, while maximizing productivity. The quality of Toyota’s products allows their customers to enjoy a high return on their investment. - Delivery is right for each customer’s order.
Toyota’s customer-driven system ensures that production output corresponds with timely delivery. Toyota’s smooth, continuous, and optimized workflows, with carefully planned and measured work-cycle times and on-demand movement of goods, allow them to consistently meet their customer’s expectations.
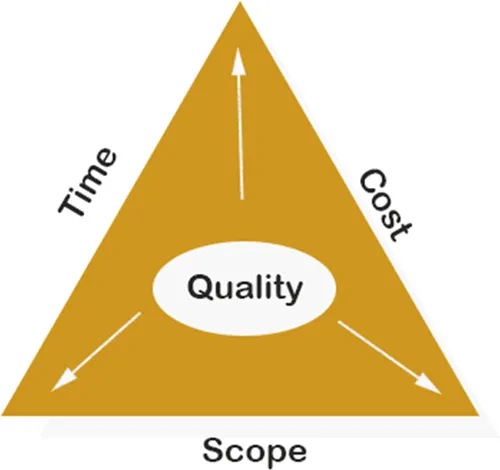
- Pull – There are three basic types of pull system: replenishment pull, sequential pull, and mixed pull system with elements of the previous two combined (see glossary at the end of chapter). In all three cases, the important technical elements for systems to succeed are: (1) flowing product in small batches (approaching one piece flow where possible); (2) pacing the processes to takt time (to stop overproduction); (3) signaling replenishment via a kanban signal; (4) leveling of product mix and quantity over time.
- Flow – A continuous flow process is a method of manufacturing that aims to move a single unit in each step of a process, rather than treating units as batches for each step.
- Takt time – Takt time is the rate at which work must be performed for customer demand to be met on time.
- Facilitates the creation of business processes that result in sustained competitive advantage in Quality, Delivery, Cost, and Innovation
- Aligns the major strategy objectives with specific resources and action plans
- Consists of a five-step process beginning with high-level strategic objectives and ends with local-level improvement targets
- Utilizes term called “Catchball” which means driving force of alignment, clarification, and employee involvement
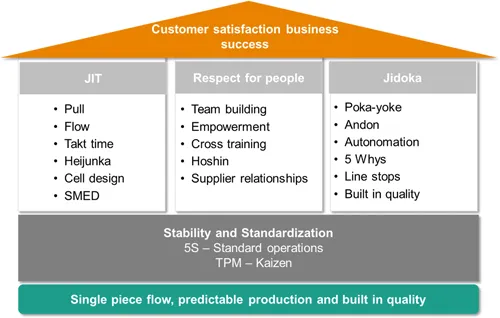
- Lean is the elimination of waste to improve the flow of information and material.
- What happens when you don’t eliminate waste?
- It adds cost to the product/service with no corresponding benefit.
- It destroys competitive advantage.
- It makes work frustrating.
- It uses valuable resources (i.e., your time) to produce no value.
- Mura is unevenness.
- Muri is overburden.
- Muda is pure waste.
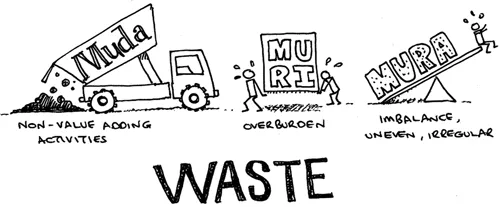
- A Japanese term for anything that is wasteful and doesn’t add value.
- Waste reduction is an effective way to increase profitability.
- Waste occurs when more resources are consumed than are necessary to produce the goods or provide the service.
- Anything that doesn’t add value to the process.
- Anything that doesn’t help create conformance to your customer’s specifications.
- Anything your c...