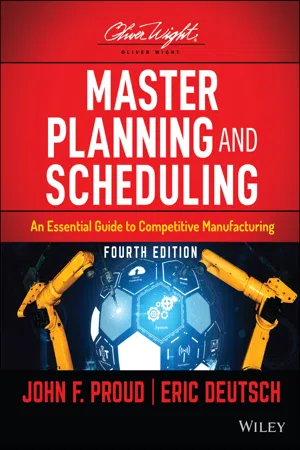
Master Planning and Scheduling
An Essential Guide to Competitive Manufacturing
John F. Proud,Eric Deutsch
- English
- ePUB (mobile friendly)
- Available on iOS & Android
Master Planning and Scheduling
An Essential Guide to Competitive Manufacturing
John F. Proud,Eric Deutsch
About This Book
Discover the practical, real-world advantages of the Oliver Wight master planning and scheduling methodology.
The newly revised Fourth Edition of Master Planning and Scheduling: An Essential Guide to Competitive Manufacturing delivers a masterful exploration of today's master planning and scheduling techniques, as well as an insightful discussion of the future of the master planning and scheduling processes and profession.
Written in the context of an ever-evolving digital environment and augmented with new and critical information required to implement best practices, the book is a guide for practitioners and leaders on the principles of master planning and scheduling and its application in modern and future work environments.
In this book, readers will learn:
- Insights regarding top-down, bottom-up, and side-to-side integration of business practices in support of a company's strategic direction and tactical deployment
- The critical link between time-phased integrated business planning, master planning, master scheduling, capacity planning, and material planning
- "How-to" details and examples to support master planning and scheduling implementation and enhancements within the company's demand and supply organizations
Master Planning and Scheduling is an indispensable guide for supply chain professionals, planners and schedulers in all functional domains of a business. It also belongs on the bookshelves of any executive or manager who seeks to improve their understanding of best practice planning and scheduling processes and how those processes enable a business to outperform the competition through alignment, integration and synchronization across all functions in an organization.
Frequently asked questions
1
Chaos in Manufacturing
A TYPICAL SITUATION IN TODAY'S MANUFACTURING WORLD
- The Place: A typical worldâwide manufacturing company
- The Time: 10:00 a.m.
- The Date: Friday, the last day of the month
- Admitting that problems, some serious, exist, and that the current situation is not healthy for the company or the people who work in it;
- Identifying the specific problemsânot just the symptoms;
- Determining the cause of the problems;
- Creating and acting on efficient and effective solutions.
Problems in Manufacturing
Symptoms of Master Planning and Scheduling Problems | |
---|---|
Uncontrollable costs | Hot lists |
Disruptions on the shop floor | Frequent schedule changes |
Late deliveries to customers | Many fullâtime expediters |
Late deliveries from suppliers | Customer complaints |
Unplanned overtime/offâloading | Many âpast dueâ orders and plans |
High workâinâprocess | Long queues |
Mismatched inventories | Endâofâmonth crunch |
Over/underutilized resources | Finger pointing/low morale |