
eBook - ePub
The Home Blacksmith
Tools, Techniques, and 40 Practical Projects for the Home Blacksmith
Ryan Ridgway
This is a test
Share book
- 250 pages
- English
- ePUB (mobile friendly)
- Available on iOS & Android
eBook - ePub
The Home Blacksmith
Tools, Techniques, and 40 Practical Projects for the Home Blacksmith
Ryan Ridgway
Book details
Book preview
Table of contents
Citations
About This Book
Geared toward answering the many questions that new blacksmiths often have, author Ryan Ridgway hopes to fill the void of inaccessible information for aspiring blacksmiths with this comprehensive volume. By explaining the physics of moving metal, the different styles of anvils and forges, and alternative fuel sources, Ridgway sets his book apart from less detailed volumes. With 40 practical, easy-to-follow projects, The Home Blacksmith shows hopeful blacksmiths how to make tools, such as hammers and chisels; farm implements, such as gate latches and hoof picks; and items for home use, including drawer pulls and candle holders.
Frequently asked questions
How do I cancel my subscription?
Can/how do I download books?
At the moment all of our mobile-responsive ePub books are available to download via the app. Most of our PDFs are also available to download and we're working on making the final remaining ones downloadable now. Learn more here.
What is the difference between the pricing plans?
Both plans give you full access to the library and all of Perlegoâs features. The only differences are the price and subscription period: With the annual plan youâll save around 30% compared to 12 months on the monthly plan.
What is Perlego?
We are an online textbook subscription service, where you can get access to an entire online library for less than the price of a single book per month. With over 1 million books across 1000+ topics, weâve got you covered! Learn more here.
Do you support text-to-speech?
Look out for the read-aloud symbol on your next book to see if you can listen to it. The read-aloud tool reads text aloud for you, highlighting the text as it is being read. You can pause it, speed it up and slow it down. Learn more here.
Is The Home Blacksmith an online PDF/ePUB?
Yes, you can access The Home Blacksmith by Ryan Ridgway in PDF and/or ePUB format, as well as other popular books in Technology & Engineering & Technical & Manufacturing Trades. We have over one million books available in our catalogue for you to explore.
Information
Chapter 1: Understanding Blacksmithing Basics
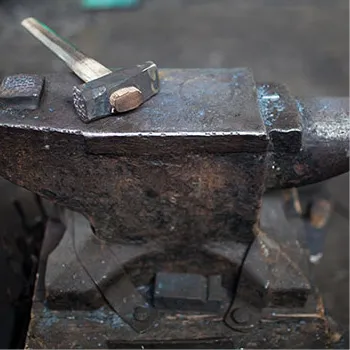
A Brief History of Blacksmithing
For new blacksmiths, knowing how our craft has evolved is extremely important in helping you set up your first forge without a lot of cost and time spent looking for materials. Ask a number of blacksmiths from around the world what the tools in a blacksmithâs forge should look like, and you will get a dozen different answers. This is because, over time, blacksmithing tools have evolved differently in different parts of the world. Ask a North American or European smith what an anvil should look like, and he or she will describe a stereotypical London-pattern anvil with a horn and a heel, straight from the cartoons. At the same time, an Asian smith may say that it is simply a square block of steel. If you went back to the Middle Ages, a European smith would give you the same answer as the Asian smith. Go back even further and any smith would point to a large, flat rock.
Today, beginner Western blacksmiths get caught up trying to find a London-pattern anvil, thinking that it is the only style of anvil that will work. This often leads to frustration, which can further lead a blacksmith to either purchase an inferior cast-iron anvil from the local welding shop or spend too much money when a simple block of steel would work. Others will spend more time looking for a good piece of railway steel, which has become the ubiquitous makeshift beginner anvil. I have used everything from Peter Wright and Hay-Budden anvils to simple steel cutoffs and hydraulic shafts stood on end. The railway anvils I have used are often as bad as cast iron because they donât have the proper mass underneath the hammering surface to support heavy forging, instead flexing and absorbing too much of your hammerâs blow.

I discuss in more detail what to look for in an anvil in a later chapter, but I feel that a little blacksmithing history will help you choose your tools more easilyâalong with the understanding that it isnât the tools that make you a blacksmith, but rather the techniques. Blacksmithsâ tools have changed with the need for and availability of fuel, iron, and science. Your forge can be the same: an evolution based on necessity and availability.
By around 1200 BC, iron was becoming the principal metal for tools and weapons, with some overlapping of the Bronze Age. Prior to this time, iron artifacts were scarce as different cultures experimented with the newly discovered technology. While iron is stronger and makes longer lasting tools, it was slow to become a commonly used metalâand eventually overtake bronzeâbecause it was more difficult to produce iron from its rock ore, and it needed higher temperatures to work. Eventually, civilizations advanced their iron-smelting technologies and began using iron for more items, including art. Iron improved a societyâs production, agricultural, and warfare abilities, and the blacksmith was considered the king of craftsmen because he created the tools for all other trades.
Each area of the world started forging iron with similar tools, likely either rocks or bronze hammers and the same anvils or boulders that they had been using to work bronze and copper. Until relatively recently, in the grand scheme of things, blacksmiths used blocks of steel or stake anvils and hammers that were fairly similar. Around the 1600s, Western European blacksmiths began to develop an anvil shape that most smiths are familiar with: the London or Continental pattern anvil. Unfortunately, this change from centuries past creates many issues for new blacksmiths today because usable antique anvils are hard to find and can be expensive, while good-quality new anvils are even more expensive. All the while, the original anvil shapeâa simple block of steelâsits in the scrap yard, waiting to be melted down and recycled.
The forge is another part of the blacksmithâs shop that has changed significantly over the past centuries, both in design and in fuel source. An early forge was simply a fire pit fueled by charcoal, and the air supply was likely a pair of leather sacs opened and closed by the blacksmithâs assistant, with a wooden or reed pipe connecting the bellows to the fire pit. Over time, this side-draft forge was raised off the ground, and different styles of bellows evolved in different regions.
Eventually, as coal became a more prevalent fuel, bottom-blast forges with blast pipes (tuyeres), known as duck-nest tuyeres, became more common and were often sold in mail-order catalogs. Modern blacksmiths now have access to other forge fuels, such as propane and acetylene, as well as electric induction. Later in the book, I will go deeper into the different forge fuels and how to make your own charcoal so that you donât waste time and money trying to find and buy blacksmithing coal.
Historically, blacksmiths forged pure iron, known as wrought iron. Wrought iron was created from iron ore with very little added carbon. These days, it is difficult to purchase pure wrought iron, so most blacksmiths use what is known as mild steel, a low-carbon steel alloy. Because of this, many smiths use the term âironâ for mild steel because it has replaced pure wrought iron as the most common metal for blacksmithing. This terminology allows for a differentiation between steel, which has enough carbon to harden properly for tools, and mild steel, which will not harden. Because you will be making your own tools for the forge and around the house and farm, this is an important distinction.
Now that you are armed with a brief history of what tools and fuels blacksmiths commonly used in the past, we can move on to understanding how metal moves. Once you understand how metal behaves when itâs forged, you can find many unconventional tools in scrap yards, just like the blacksmiths of old had to.
Same Techniques, Different Times
Did You Know?
The Physics of Moving Metal
Before we get into finding tools and the actual techniques of blacksmithing, it will be helpful to look at how iron behaves when forged, so that we can start to understand how the variously shaped tools move metal. By learning how shapes, rather than specific tools, move metal, your eyes will be opened as you wander through your local scrap yard. In my experience, most beginning blacksmiths end up reading a beginnerâs blacksmithing book that leads off with a description of the tools in a typical post-1800s blacksmith shop that used coalâand then the new blacksmith spends all of his or her time searching for the tools in the book. Instead, new blacksmiths need to understand how metal can be controlled and then find the tools that have the shapes to do it. This makes setting up a shop much easier.
The great thing about iron is its immense strength when cool and ...