
The Repair of Vehicle Bodies
Andrew Livesey
- 530 Seiten
- English
- ePUB (handyfreundlich)
- Ăber iOS und Android verfĂŒgbar
The Repair of Vehicle Bodies
Andrew Livesey
Ăber dieses Buch
The revised and updated seventh edition of this best-selling reference manual on vehicle body repair brings the book up to date for the current body repair trade. It serves as a comprehensive guide covering the vocationally related qualification (VRQ) required by the modern student and apprentice, as well as providing the CPD essential for all working professionals.
The entire book is overhauled to reflect current industry trends with regards to materials, processes and procedures. New additions include:
-
- An entirely new section on the work of the MET technician (mechanical, electrical and trim)
-
- New developments in body repair methodology such as repair pods and the greater use of alignment equipment
-
- Greater emphasis on the environment with new sections on hybrid vehicles and the hazards of starting current vehicles with high levels of technology
-
- Details on both the historic and the current joining methods for the vintage and modern markets
-
- Full coverage on the legalities surrounding insurance work for bodyshop staff
-
- Updated tables and illustrations
This book not only provides the knowledge and skills for body repair, it helps to develop a real understanding of the how and why behind this information. It will be essential for anyone studying Levels 1-3 Vehicle Body Repair, Vehicle Refinishing and MET courses, including the new apprenticeships and technical certificates from the IMI, Pearson-BTEC and C&G. HNC and degree Automotive Engineering students will find the text valuable to develop skills and knowledge for practical project work. Industry professionals, vehicle restorers and car DIY enthusiasts will continue to find it an essential and comprehensive source of information.
HĂ€ufig gestellte Fragen
Information
1
Car body construction
Starting out
Vehicle safety testing
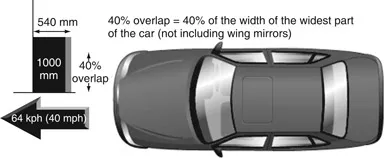
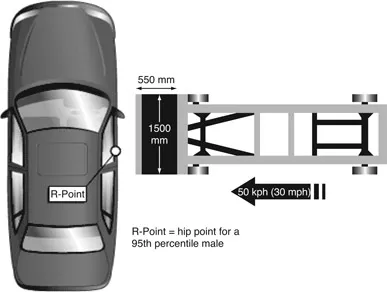
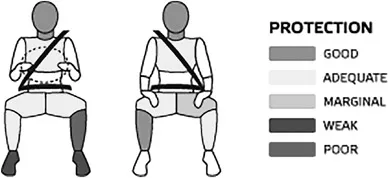
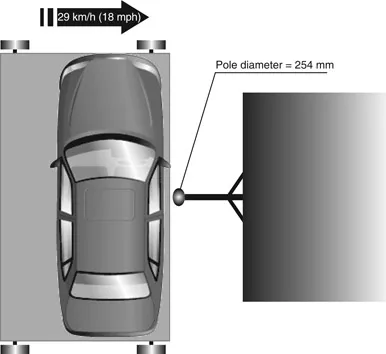
- Frontal impact test â the test for frontal impact is carried out at 64 kph (40 mph). The car strikes a deformable barrier which is offset from the centre. This is similar to many road accidents in which one car strikes another during an over taking accident or strikes another object like a road bollard.
- Side impact test â this is similar to many accidents in which one car is hit in the side by another â often referred to as âT-boningâ after the shape of a piece of steak. The deformable trolley is towed on rails into the driverâs side of the car at 50 kph (30 mph), typical of accidents at road junctions.
- Pole test â about a quarter of all serious or fatal accidents happen because of side impacts. The car being tested is propelled sideways on a trolley at 29 kph (18 mph) into a rigid pole. The pole is similar in size to a telegraph pole or lamppost. The main reason for this test is to assess head injury to the driver. The roof strength and operation of side airbags are important to prevent head injury.
- Pedestrian impact tests â a series of tests are carried out to replicate accidents involving both child and adult pedestrian impact at 40 kph (25 mph). This speed is now being adopted as a maximum in high-density build-up areas to reduce pedestrian deaths. This series of tests has led to vehicles having smooth rounded fronts with the absence of bonnet badges or other protruding features.
- Star ratings â each vehicle which is tested is given a star rating for its protection of adult occupant, child occupant and pedestrians. The star ratings are made up from points scoring against each test. The ratings of current vehicles can be found on the EuroNCAP website www.euroncap.com.
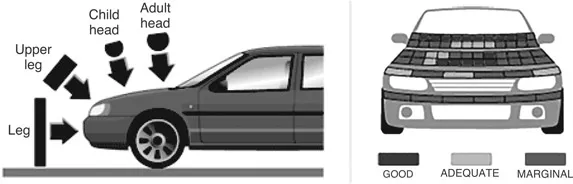
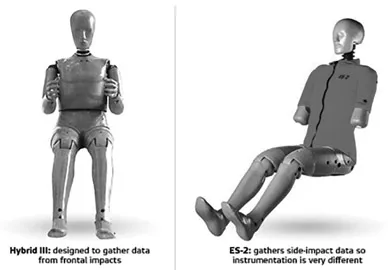
Elements of vehicle construction
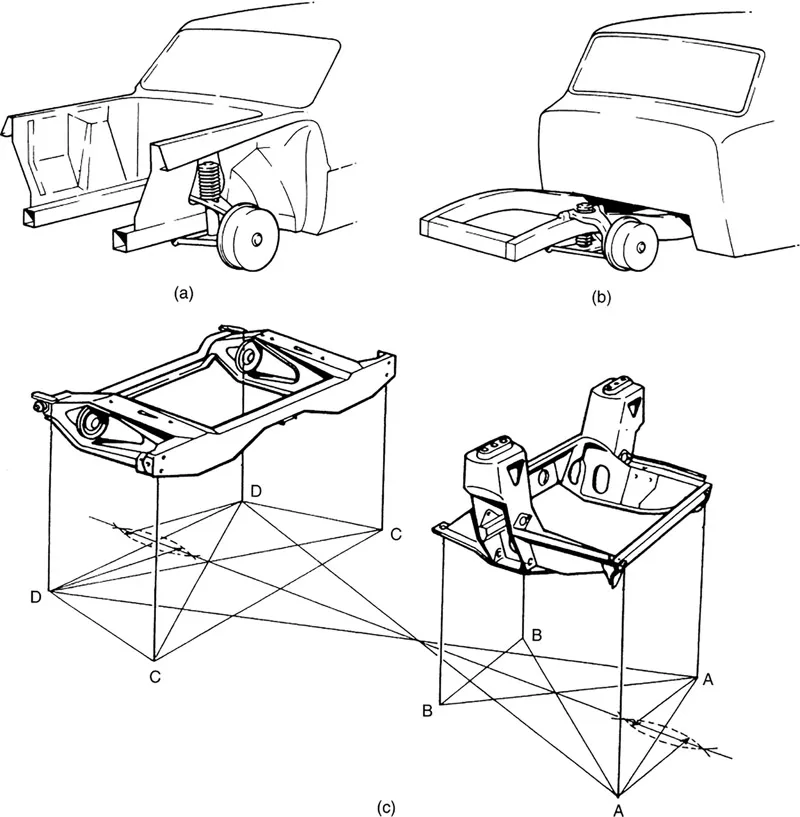