
eBook - ePub
Mechatronic Systems
Devices, Design, Control, Operation and Monitoring
Clarence W. de Silva, Clarence W. de Silva
This is a test
Buch teilen
- 496 Seiten
- English
- ePUB (handyfreundlich)
- Über iOS und Android verfügbar
eBook - ePub
Mechatronic Systems
Devices, Design, Control, Operation and Monitoring
Clarence W. de Silva, Clarence W. de Silva
Angaben zum Buch
Buchvorschau
Inhaltsverzeichnis
Quellenangaben
Über dieses Buch
Mechatronics has emerged as its own discipline over the past decade, yet no reference has lived up to the demands of being a working guide for designing and implementing the new generation of mechatronic systems. Uniting an international team of leading experts, Mechatronic Systems: Devices, Design, Control, Operation and Monitoring rises to the ch
Häufig gestellte Fragen
Wie kann ich mein Abo kündigen?
Gehe einfach zum Kontobereich in den Einstellungen und klicke auf „Abo kündigen“ – ganz einfach. Nachdem du gekündigt hast, bleibt deine Mitgliedschaft für den verbleibenden Abozeitraum, den du bereits bezahlt hast, aktiv. Mehr Informationen hier.
(Wie) Kann ich Bücher herunterladen?
Derzeit stehen all unsere auf Mobilgeräte reagierenden ePub-Bücher zum Download über die App zur Verfügung. Die meisten unserer PDFs stehen ebenfalls zum Download bereit; wir arbeiten daran, auch die übrigen PDFs zum Download anzubieten, bei denen dies aktuell noch nicht möglich ist. Weitere Informationen hier.
Welcher Unterschied besteht bei den Preisen zwischen den Aboplänen?
Mit beiden Aboplänen erhältst du vollen Zugang zur Bibliothek und allen Funktionen von Perlego. Die einzigen Unterschiede bestehen im Preis und dem Abozeitraum: Mit dem Jahresabo sparst du auf 12 Monate gerechnet im Vergleich zum Monatsabo rund 30 %.
Was ist Perlego?
Wir sind ein Online-Abodienst für Lehrbücher, bei dem du für weniger als den Preis eines einzelnen Buches pro Monat Zugang zu einer ganzen Online-Bibliothek erhältst. Mit über 1 Million Büchern zu über 1.000 verschiedenen Themen haben wir bestimmt alles, was du brauchst! Weitere Informationen hier.
Unterstützt Perlego Text-zu-Sprache?
Achte auf das Symbol zum Vorlesen in deinem nächsten Buch, um zu sehen, ob du es dir auch anhören kannst. Bei diesem Tool wird dir Text laut vorgelesen, wobei der Text beim Vorlesen auch grafisch hervorgehoben wird. Du kannst das Vorlesen jederzeit anhalten, beschleunigen und verlangsamen. Weitere Informationen hier.
Ist Mechatronic Systems als Online-PDF/ePub verfügbar?
Ja, du hast Zugang zu Mechatronic Systems von Clarence W. de Silva, Clarence W. de Silva im PDF- und/oder ePub-Format sowie zu anderen beliebten Büchern aus Technology & Engineering & Electrical Engineering & Telecommunications. Aus unserem Katalog stehen dir über 1 Million Bücher zur Verfügung.
Information
1
Technology Needs for Mechatronic Systems
1.1 Introduction.................................................1-1 | |
1.2 Mechatronic System Technologies.........1-2 | |
1.3 Intelligent Mechatronic Devices.............1-4 | |
1.4 Modeling and Design..............................1-6 | |
1.5 Mechatronic Design Concept..................1-7 | |
Mechatronic Design Quotient (MDQ) | |
1.6 Evolution of Mechatronics......................1-9 | |
1.7 Application Areas..................................1-10 | |
1.8 Conclusion.............................................1-10 | |
C.W. de Silva | References.........................................................1-11 |
Summary
Mechatronics is a multidisciplinary engineering field which involves a synergistic integration of several areas such as mechanical engineering, electrical and electronic engineering, control engineering, and computer engineering. In this chapter the field of mechatronics is introduced, the technology needs for such systems are indicated, and some important issues in the design and development of a mechatronic product or system are highlighted. Technologies of sensing, actuation, signal conditioning, interfacing, communication, and control are particularly important for mechatronic systems. Intelligent mechatronic systems require further technologies for representation and processing of knowledge and intelligence, and particularly those technologies that impart intelligent characteristics to the system. The design and development of a mechatronic system will require an integrated and concurrent approach to deal with the subsystems and subprocesses of a multidomain (mixed) system. The subsystems of a mechatronic system should not be designed or developed independently without addressing the system integration, subsystem interactions and matching, and the intended operation of the overall system. Such an integrated and concurrent approach will make a mechatronic design more optimal than a conventional design. In this chapter, some important issues in the design and development of a mechatronic product or system are highlighted.
1.1 Introduction
The subject of mechatronics concerns the synergistic application of mechanics, electronics, controls, and computer engineering in the development of electromechanical products and systems, through an integrated design approach [1]. A mechatronic system will require a multidisciplinary approach for its design, development, and implementation. In the traditional development of an electromechanical system, the mechanical components and electrical components are designed or selected separately and then integrated, possibly with other components, and hardware and software. In contrast, in the mechatronic approach, the entire electromechanical system is treated concurrently in an integrated manner by a multidisciplinary team of engineers and other professionals. Naturally, a system formed by interconnecting a set of independently designed and manufactured components will not provide the same level of performance as a mechatronic system, which employs an integrated and concurrent approach for design, development, and implementation [2]. The main reason is straightforward. The best match and compatibility between component functions can be achieved through an integrated and unified approach to design and development, and best operation is possible through an integrated implementation. Generally, a mechatronic product will be more efficient and cost effective, more precise and accurate, more reliable, more flexible and functional, and less mechanically complex, compared to a nonmechatronic product that needs a similar level of effort in its development. Performance of a nonmechatronic system can be improved through sophisticated control, but this is achieved at an additional cost of sensors, instrumentation, and control hardware and software, and with added complexity and control burden. Mechatronic products and systems include modern automobiles and aircraft, smart household appliances, medical robots, space vehicles, and office automation devices. In this chapter, some important issues in the design and development of a mechatronic product or system will be highlighted and the associated technology needs will be indicated.
1.2 Mechatronic System Technologies
A typical mechatronic system consists of a mechanical skeleton, actuators, sensors, controllers, signal conditioning/modification devices, computer/digital hardware and software, interface devices, and power sources. Different types of sensing, and information acquisition and transfer are involved among all these various types of components. For example, a servomotor, which is a motor with the capability of sensory feedback for accurate generation of complex motions, consists of mechanical, electrical, and electronic components (see Figure 1.1). The main mechanical components are the rotor and the stator. The electrical components include the circuitry for the field windings and rotor windings (not in the case of permanentmagnet rotors, as shown in Figure 1.1), and circuitry for power transmission and commutation (if needed). Electronic components include those needed for sensing, (e.g., optical encoder for displacement and speed sensing, and tachometer for speed sensing) [3].

FIGURE 1.1 Brushless dc servomotor is a mechatronic device.
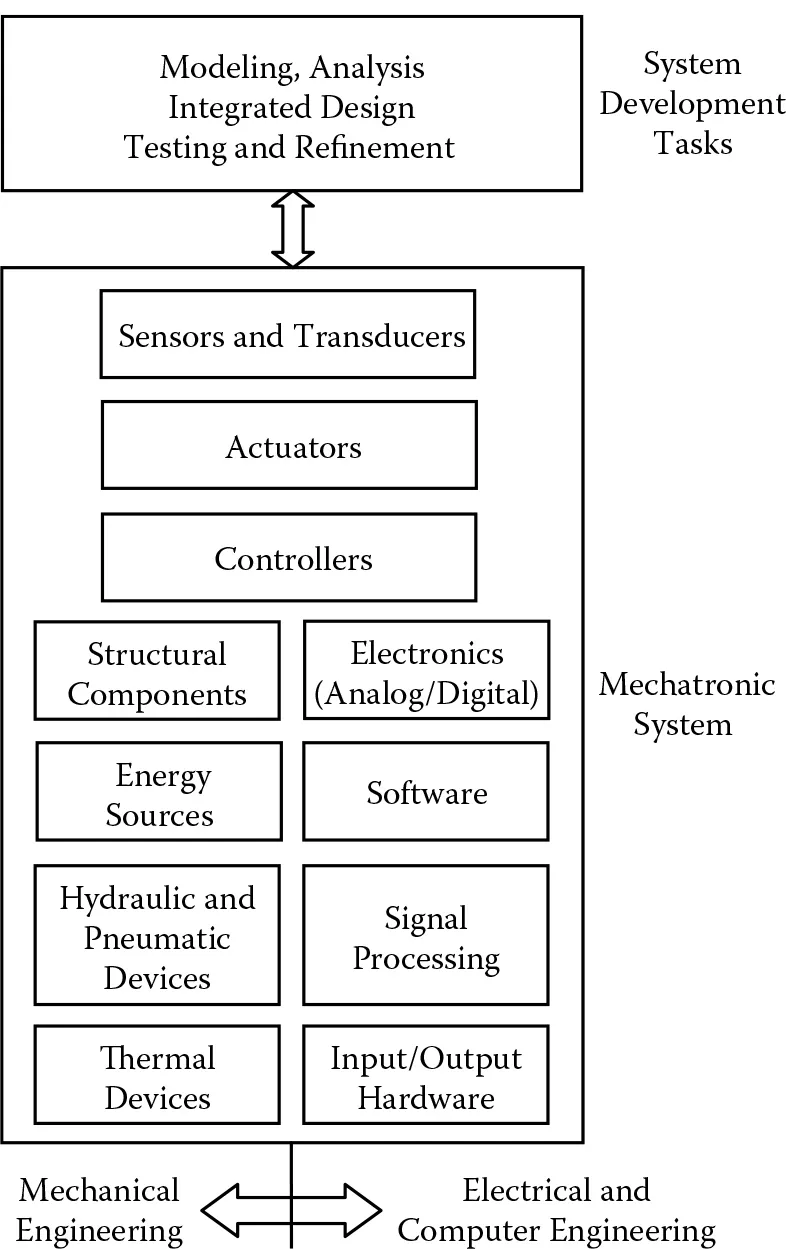
FIGURE 1.2 Technologies in a general mechatronic system.
Technology issues and needs of a general mechatronic system are indicated in Figure 1.2. It is seen that they span the traditional fields of mechanical engineering, electrical and electronic engineering, control engineering, and computer engineering. Each aspect or issue within the system may take a multidomain character. For example, as noted before, an actuator (e.g., DC servomotor) itself may represent a mechatronic device within a larger mechatronic system such as an automobile or a robot.
A mechatronic system may be treated as a control system, consisting of a plant (which is the process, machine, device, or system to be controlled), actuators, sensors, interfacing and communication structures, signal modification devices, and controllers and compensators. The function of the mechatronic system is primarily centered at the plant. Actuators, sensors, and signal modification devices might be integral with the plant itself, or might be needed as components that are external to the plant, for proper operation of the overall mechatronic system. The controller is an essential part of a mechatronic system. It generates control signals to the actuators in order to operate (drive) the plant in a desired manner. Sensed signals might be used for system monitoring and feedforward control, in addition to feedback control. These various components may not be present as physically separate and autonomous units in a mechatronic system in general, even though they may be separately identified from a functional point of view. For example, an actuator and a sensor might be an integral part of the plant itself.
As an example, consider a robotic manipulator. The joint motors are usually considered as a part of the manipulator because, from the perspective of robot dynamics, it is virtually impossible to uncouple the actuators from the main structure of the robot. Specifically, the torque transmitted to a manipulator link will depend on the (magnetic) torque of the motor at that joint as well as on the motor speed. Furthermore, magnetic torque will depend on the back e.m.f. in the rotor, which in turn will be determined by the motor speed. The transmitted torque will determine the link motion (displacement, speed, and acceleration), which is directly related to the motor motion (say, through a gear ratio). In the presence of such dynamic coupling, it is not proper to treat the actuator as a component external to the plant. However, the sensors (e.g., tachometers and encoders) at the joints can be treated separately from the plant because their dynamic coupling with the manipulator structure is usually negligible.
For a mechatronic system, design technologies are as important as the instrumentation technologies previously mentioned. In fact, in some situation, the design of a mechatronic system may be interpreted as the process of integrating (physical/functional) components such as actuators, sensors, signal modification devices, interfacing and communicating structures, and controllers with a plant so that the plant in the overall mechatronic system will respond to inputs (or commands) in a desired manner. From this point of view, design is an essential procedure in the instrumentation of a mechatronic system. The instrumentation will include the design of a component structure (including addition and removal of components and interconnecting them into various structural forms and locations), selection of components (giving consideration to types, ratings, and capacities), interfacing various components (perhaps through signal modification devices, properly considering impedances, signal types and signal levels), adding controllers and compensators (including the selection of a control structure), implementing control algorithms, and tuning (selecting and adjusting the unknown parameters of) the overall mechatronic system. Many of these instrumentation tasks are also design tasks.
In a true mechatronic sense, the design of a multidomain multicomponent system of the nature identified in Figure 1.2 will require simultaneous consideration and integrated design of all its components. Such an integrated and “concurrent” design will call for a fresh look at the design process itself, and also a formal consideration of information and energy transfer between components within the system. It is expected that the mechatronic approach will result in higher quality of products and services, improved performance, and increased reliability, approaching some form of optimality. This will enable the development and production of electromechanical systems efficiently, rapidly, and economically. Relevant technologies for mechatronic engineering should concern all stages of design, development, integration, instrumentation, control, testing, operation, and maintenance of a mechatronic system.
When performing an integrated design of a mechatronic system, the concepts of energy/power present a unifying thread. The reasons are clear. First, in an electromechanical system, ports of power/energy exist, which link electrical dynamics and mechanical dynamics. Hence, modeling, analysis, and optimization of a mechatronic system can be carried out using a hybrid-system (or mixed-system, or multidomain system) formulation (a model) that integrates mechanical aspects and electrical aspects of the system. Second, an optimal design will aim for minimal energy dissipation and maximum energy efficiency. There are related implications; for example, greater dissipation of energy will mean reduced overall efficiency and increased thermal problems, noise, vibration, malfunctions, and wear and tear. Again, a hybrid model that presents an accurate picture of energy/power flow within the system will provide an appropriate framework for the mechatronic design.
By definition, a mechatronic design should result ...