
eBook - ePub
Bearing Capacity Of Roads
A. Gomes Correia
This is a test
Condividi libro
- 800 pagine
- English
- ePUB (disponibile sull'app)
- Disponibile su iOS e Android
eBook - ePub
Bearing Capacity Of Roads
A. Gomes Correia
Dettagli del libro
Anteprima del libro
Indice dei contenuti
Citazioni
Informazioni sul libro
This book is an outcome of the sixth conference on bearing capacity of roads and airfield held in Lisbon, Portugal. It focuses on railway tracks and covers following topics: bearing capacity policies, concepts, costs and condition surveys; analysis and modelling; design and environmental effects.
Domande frequenti
Come faccio ad annullare l'abbonamento?
È semplicissimo: basta accedere alla sezione Account nelle Impostazioni e cliccare su "Annulla abbonamento". Dopo la cancellazione, l'abbonamento rimarrà attivo per il periodo rimanente già pagato. Per maggiori informazioni, clicca qui
È possibile scaricare libri? Se sì, come?
Al momento è possibile scaricare tramite l'app tutti i nostri libri ePub mobile-friendly. Anche la maggior parte dei nostri PDF è scaricabile e stiamo lavorando per rendere disponibile quanto prima il download di tutti gli altri file. Per maggiori informazioni, clicca qui
Che differenza c'è tra i piani?
Entrambi i piani ti danno accesso illimitato alla libreria e a tutte le funzionalità di Perlego. Le uniche differenze sono il prezzo e il periodo di abbonamento: con il piano annuale risparmierai circa il 30% rispetto a 12 rate con quello mensile.
Cos'è Perlego?
Perlego è un servizio di abbonamento a testi accademici, che ti permette di accedere a un'intera libreria online a un prezzo inferiore rispetto a quello che pagheresti per acquistare un singolo libro al mese. Con oltre 1 milione di testi suddivisi in più di 1.000 categorie, troverai sicuramente ciò che fa per te! Per maggiori informazioni, clicca qui.
Perlego supporta la sintesi vocale?
Cerca l'icona Sintesi vocale nel prossimo libro che leggerai per verificare se è possibile riprodurre l'audio. Questo strumento permette di leggere il testo a voce alta, evidenziandolo man mano che la lettura procede. Puoi aumentare o diminuire la velocità della sintesi vocale, oppure sospendere la riproduzione. Per maggiori informazioni, clicca qui.
Bearing Capacity Of Roads è disponibile online in formato PDF/ePub?
Sì, puoi accedere a Bearing Capacity Of Roads di A. Gomes Correia in formato PDF e/o ePub, così come ad altri libri molto apprezzati nelle sezioni relative a Technology & Engineering e Civil Engineering. Scopri oltre 1 milione di libri disponibili nel nostro catalogo.
Informazioni
Analysis and modeling
A Simple Damage Approach to Modelling Fatigue in Bituminous Materials
DOI:10.1201/9781003078814-11
ABSTRACT: Results from laboratory fatigue testing indicate that the effective stiffness modulus of asphaltic material can be reduced significantly under repeated loading without the presence of visible cracking. This indicates that damage is accumulating in the asphaltic material thus reducing the effective volume able to carry the applied load (and hence reducing the effective stiffness modulus). Damage mechanics characterises the state of a material under mechanical loading by a dimensionless scalar variable (known as damage). This paper describes the application of continuum damage mechanics in a simple way to model fatigue of asphalt mixtures. A specimen for uniaxial testing has been developed and a set of stress controlled fatigue tests have been performed over a range of temperatures and stress levels. The results have been used to determine a simple evolution law for the rate of damage accumulation. Trapezoidal cantilever (2-point bend) tests have also been performed and the results have been compared to results from the uniaxial test.
KEYWORDS: Damage mechanics, fatigue cracking, stiffness reduction, uniaxial test
1 INTRODUCTION
There are many different approaches to modelling fatigue and fracture in bituminous materials, ranging from simple models (e.g. tensile strain) to more complicated approaches using fracture mechanics and damage mechanics. Traditionally, fatigue is divided into two stages; crack initiation and crack propagation. Crack initiation has been defined as the growth and coalescence of microcracks and crack propagation has been defined as the growth of macro-cracks (Suresh, 1991). Results from laboratory fatigue testing and full-scale accelerated trials indicate that the effective stiffness modulus of an asphaltic material can be reduced significantly under repeated loading without the presence of visible cracking. This indicates that damage is accumulating in the material thus reducing the effective volume able to carry the applied load (and hence reducing the effective stiffness modulus).
Continuum damage mechanics evolved in the 1960s as a way of representing the collective effect of crack-like defects on deterioration under mechanical loading (Lemaitre, 1996). Typically, the state of a material is characterised by a dimensionless scalar variable (known as damage) which ranges from 0 (undamaged) to 1 (fully damaged). This paper describes the application of continuum damage mechanics in a simple way to model fatigue of asphalt mixtures.
2 DAMAGE MECHANICS
From damage mechanics concepts, the internal damage to a body can be expressed in terms of a reduction in the effective area under uniaxial conditions (Kachanov, 1986), as follows:
(1)
where AD = area of flaws and A = area of the whole plane. It is clear that D is bounded by 0 (undamaged) and 1 (fully broken in two parts).
It was suggested by Lemaitre (1996) that the above equation should be re-expressed in terms of elastic (Young’s) modulus. For pavement engineering applications, the stiffness modulus can be used as follows:
(2)
where Se is effective stiffness modulus; and S is modulus of the intact material.
Assuming the internal damage gradually evolves as the number of loading cycles increases, the rate of damage growth per cycle could be expressed as a function of some critical parameters which represent the material characteristics and testing conditions, as follows:
(3)
where a is stress, ɛ is strain and T temperature.
3 UNIAXIAL FATIGUE TESTS
Data from uniaxial fatigue tests can be used to develop the function f in Equation 3 for one dimensional stress conditions. However, one of the most difficult aspects of the uniaxial fatigue test is the uncertainty of the failure position. A predictable failure position is necessary to measure accurate physical properties and to obtain reliable and stable test results. Therefore, a specimen with a necked central section has been developed. Figure 1 shows the details of the specimen geometry.
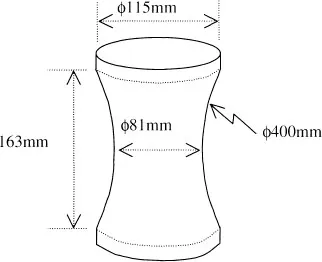
A mixture based on the specification for a 14 mm close graded wearing course Dense Bitumen Macadam (DBM) was selected for the test programme (BS 4987, 1988). Limestone aggregates and a 50 pen grade of bitumen were used in the mixture. The specimens were manufactured using a specially designed mould. A combination of static and vibratory compaction was used to achieve the required specimen density (air void content). After compaction the specimens were placed in the uniaxial testing machine (see Fig. 2) where they were subjected to sinusoidal loading (load control) at a frequency of 10 Hz.
Two Linear Variable Differential Transformers (LVDTs) were attached to the specimens (at diametrically opposite locations) to measure displacements over the central 60 mm of the necked section. The two LVDT readings were averaged and divided by the gauge length (60 mm) to provide a local strain measurement. A load cell was used to measure the applied force. The stress acting on the central section of the specimen was calculated and divided by the local strain to determine the stiffness modulus of the material. The test was continued until the specimen failed.
3.1 Investigation of Fatigue Behaviour
Figure 3 shows a typical set of stiffness modulus results plotted as a function of number of load a...