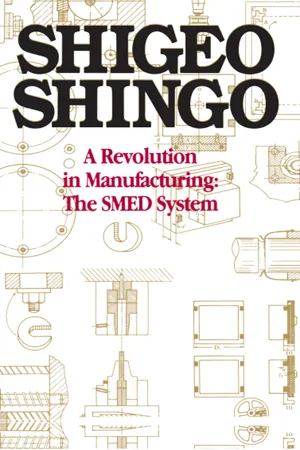
eBook - ePub
A Revolution in Manufacturing
The SMED System
Shigeo Shingo
This is a test
Buch teilen
- 384 Seiten
- English
- ePUB (handyfreundlich)
- Über iOS und Android verfügbar
eBook - ePub
A Revolution in Manufacturing
The SMED System
Shigeo Shingo
Angaben zum Buch
Buchvorschau
Inhaltsverzeichnis
Quellenangaben
Über dieses Buch
Written by the industrial engineer who developed SMED (single-minute exchange of die) for Toyota, A Revolution in Manufacturing provides a full overview of this powerful just in time production tool. It offers the most complete and detailed instructions available anywhere for transforming a manufacturing environment in ways that will speed up produ
Häufig gestellte Fragen
Wie kann ich mein Abo kündigen?
Gehe einfach zum Kontobereich in den Einstellungen und klicke auf „Abo kündigen“ – ganz einfach. Nachdem du gekündigt hast, bleibt deine Mitgliedschaft für den verbleibenden Abozeitraum, den du bereits bezahlt hast, aktiv. Mehr Informationen hier.
(Wie) Kann ich Bücher herunterladen?
Derzeit stehen all unsere auf Mobilgeräte reagierenden ePub-Bücher zum Download über die App zur Verfügung. Die meisten unserer PDFs stehen ebenfalls zum Download bereit; wir arbeiten daran, auch die übrigen PDFs zum Download anzubieten, bei denen dies aktuell noch nicht möglich ist. Weitere Informationen hier.
Welcher Unterschied besteht bei den Preisen zwischen den Aboplänen?
Mit beiden Aboplänen erhältst du vollen Zugang zur Bibliothek und allen Funktionen von Perlego. Die einzigen Unterschiede bestehen im Preis und dem Abozeitraum: Mit dem Jahresabo sparst du auf 12 Monate gerechnet im Vergleich zum Monatsabo rund 30 %.
Was ist Perlego?
Wir sind ein Online-Abodienst für Lehrbücher, bei dem du für weniger als den Preis eines einzelnen Buches pro Monat Zugang zu einer ganzen Online-Bibliothek erhältst. Mit über 1 Million Büchern zu über 1.000 verschiedenen Themen haben wir bestimmt alles, was du brauchst! Weitere Informationen hier.
Unterstützt Perlego Text-zu-Sprache?
Achte auf das Symbol zum Vorlesen in deinem nächsten Buch, um zu sehen, ob du es dir auch anhören kannst. Bei diesem Tool wird dir Text laut vorgelesen, wobei der Text beim Vorlesen auch grafisch hervorgehoben wird. Du kannst das Vorlesen jederzeit anhalten, beschleunigen und verlangsamen. Weitere Informationen hier.
Ist A Revolution in Manufacturing als Online-PDF/ePub verfügbar?
Ja, du hast Zugang zu A Revolution in Manufacturing von Shigeo Shingo im PDF- und/oder ePub-Format sowie zu anderen beliebten Büchern aus Betriebswirtschaft & Operations. Aus unserem Katalog stehen dir über 1 Million Bücher zur Verfügung.
Information
PART ONE
Theory and Practice of the SMED System
Part One describes the background and theory of the SMED system, and provides concrete examples of improvement techniques. However, mere mastery of specific techniques is not enough to ensure the proper implementation of the SMED concept. Effective implementation in a wide variety of plant situations is possible only when we understand fully the whole range of theory, principles, practical methods, and concrete techniques that have evolved with SMED.
Chapter 1 explains the structure of production and the role of setup in the production process. All production is composed of processes and operations. When the basic elements of operations are analyzed, it is seen that setup operations occur at every stage in the manufacturing process.
Chapter 2 describes the nature and significance of setup operations carried out in the past and explains diversified, low-volume production. Combining diversified, small-lot production with SMED is the most effective way to achieve flexible production and maximum productivity.
Chapters 3, 4, 5 cover the center issues of this book by providing the theoretical framework and practical techniques of the SMED system. Chapter 3 shows how SMED evolved by distinguishing internal setup, or IED(internal exchange of die), from external setup, or OED(external exchange of die). The four conceptual stages of SMED are identified: first, IED and OED are not distinguished; then, IED and OED are distinguished; next, IED is converted to OED; and finally, all aspects of the setup are streamlined. In Chapter 4, practical techniques corresponding to these four stages are described. Significant improvements in setup time can be achieved at each stage of setup. Chapter 5 takes a closer look at improvements in internal setup operations, stressing three areas of improvement: the implementation of parallel operations, the use of functional clamps, and the elimination of adjustments.
Chapter 6 describes the application of the SMED system to metal presses and plastic forming machines. Three types of metal presses are discussed: single-shot presses, progressive die presses, and transfer die presses. Four aspects of setup on plastic forming machines are then explored: die setup, switching resins, coolant line switching, and die preheating.
Chapter 7 completes our examination of the SMED system by looking at the effects of SMED. While shortened setup times and improved work rates are primary, other results increase a company’s strategic advantage in numerous areas, including health and safety, training, costs, lead times, and inventory control.
1
The Structure of Production
A SCHEMATIC OUTLINE OF PRODUCTION
Production activities may best be understood as networks of processes and operations (Figure 1-1).
A process is a continuous flow by which raw materials are converted into finished goods. In a shaft-making operation, for example, the following sequence might be observed:
1. Store raw materials in a warehouse.
2. Transport materials to the machines.
3. Store them near the machines.
4. Process them on the machines.
5. Store the finished products near the machines.
6. Inspect the finished products.
7. Store the finished products for shipment to customers.
Although the flow would probably be more complex in a real factory, this is a valid illustration of the production process.
An operation, by contrast, is any action performed by man, machine, or equipment on raw materials, intermediate, or finished products. Production is a network of operations and processes, with one or more operations corresponding to each step in the process.
Upon further reflection it becomes apparent that manufacturing processes can be divided into four distinct phases:
1. Processing: assembly, disassembly, alteration of shape or quality.
2. Inspection: comparison with a standard
3. Transportation: change of location
4. Storage: a period of time during which no work, transportation, or inspection is performed on the product
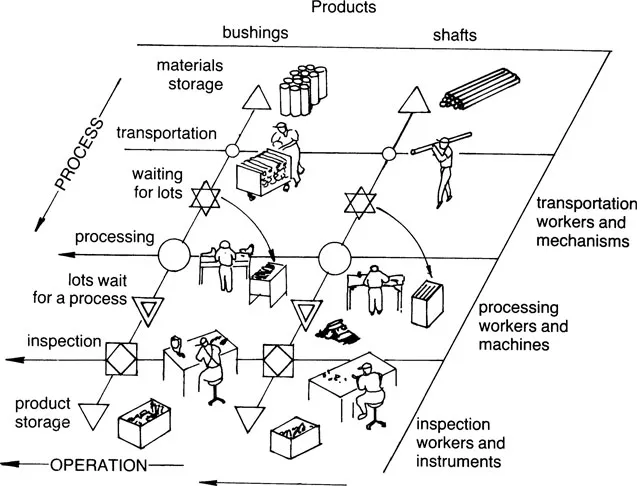
FIGURE 1-1. Structure of Production
The storage phase itself may be broken into four categories:
1. Storage of raw materials
2. Storage of the finished product
3. Waiting for a process: an entire lot waits because work on the previous lot has not yet been completed
4. Waiting for a lot: while the first item in a lot is being machined, the remaining items must wait to be processed in turn
The internal structure of an operation can also be analyzed as follows:
Preparation, after-adjustment. These operations are performed once, before and after each lot is processed. In this book they are referred to as setup operations.
Principal operations. Carried out for each item, these operations fall into three categories:
1. Essential operations: the actual machining of the material
2. Auxiliary operations: attaching workpieces to or removing them from machines
3. Margin allowances: irregularly occurring actions such as resting, drinking water, sweeping up cuttings, machinery breakdown, etc. Margin allowances can be further categorized under fatigue, hygiene, operation (performed only for a specific operation), and shopwide (performed for all operations).
Thus, there are several basic elements that combine to form operations (Figure 1-2).
THE RELATIONSHIP BETWEEN PROCESSES AND OPERATIONS
Each phase of the manufacturing process — work, inspection, transportation, and storage — has a corresponding operation. That is, there are work operations, inspection operations, transportation operations, and storage operations (Figure 1-3). Each of these operations, furthermore, has four subcategories: setup, essential, auxiliary, and margin allowance. Therefore, there are setup, essential, auxiliary, and margin allowance operations pertaining to work, inspection, transportation, and storage.
An essential operation, then, would involve, for example, the following:
• Processing operation: the actual cutting of a shaft
• Inspection operation: measuring the diameter with a micrometer
• Transportation operation: conveying a shaft to the next process
• Storage operation: storing the shaft on a rack
The same analysis applies to setup operations, whether they are processing operation setups, inspection operation setups, transportation operation setups, or storage operation setups.
Although the chief emphasis in this book will be on processing operation setups, what will be said is equally applicable to inspection, transportation and storage operations.
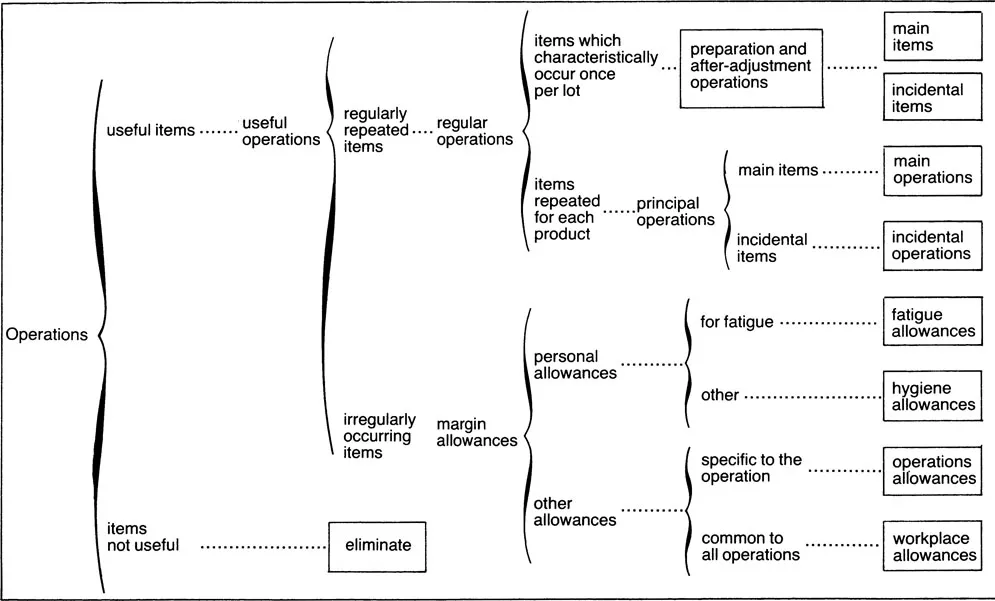
FIGURE 1-2. The Structure of Operations
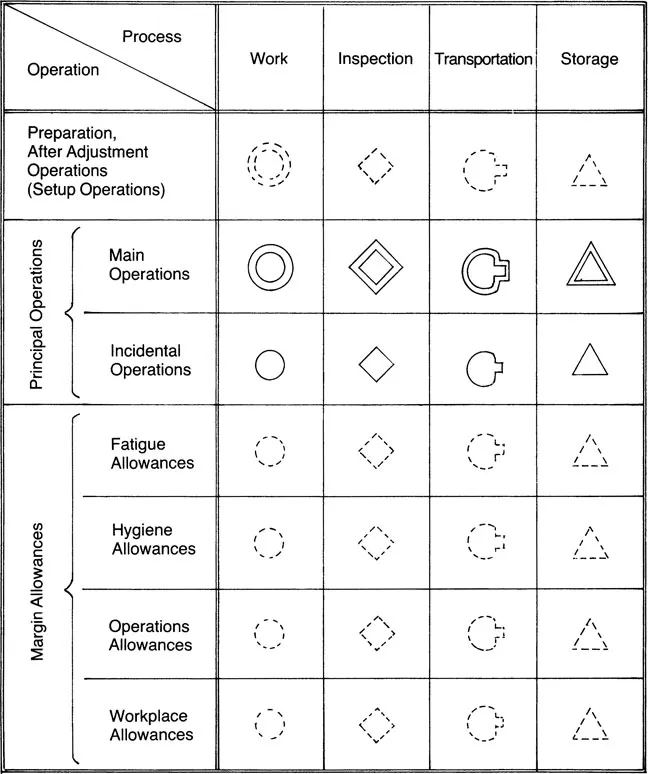
FIGURE 1-3. The Relationship Between Processes and Operations
SUMMARY
The main point of this chapter is that production activities comprise processes and operations, and setups are included in each type of operation.
2
Setup Operations in the Past
SOME DEFINITIONS OF TERMS
Small, Medium, and Large Lots
Although discussions of setup procedures often mention small, medium, and large lots, these terms are not precise and are, in fact, rather vague. For the sake of convenience, this book will use the following classification as a rough guide:
Small lot: 500 units or fewer
Medium lot: 501 to 5,000 units
Large lot: more than 5,000 units
Excess Inventory and Excess Anticipated Production
With a promised delivery date coming up fast, it would be awkward to find defective goods causing a shortage in the quantity ready for shipment. To avoid such a shortage, 330 items might be produced to satisfy an order for 300. If only twenty turn out, in fact, to be defective, then ten unnecessary items remain. If the order is not repeated, these leftover must be discarded; often they are kept in inventory with the hope of receiving another order for them. This stock, resulting from the production of too many goods, is called excess inventory.
Another type of surplus, excess anticipated production, results when intermediate or finished goods are produced before they are actually needed.
Everyone will agree that it is wasteful to dispose of surplus goods, and most managers do their best to avoid excess inventory. Strangely enough, however, goods that are produced before they are needed — excess anticipated production — often are not thought of as particularly undesirable. Indeed, some relief is often felt that a deadline has not been missed.
In this book, the terms stock and inventory will usually refer to excess anticipated producti...